Advanced Materials and Composites
Lighter & Stronger with Graphene
Technology’s rapid development imposes strict demands on material performance. As planes, cars and marine vessels move faster they experience higher static and dynamic loads. For example, the pursuit of a reduced carbon footprint is leading to the replacement of gasoline-powered engines with electric ones, while the green energy industry is looking to improve wind turbine blades. These transitions require lighter and stronger materials to be used.
For many years, carbon fiber and fiberglass composites have been proving their ability to replace conventional materials such as metal, wood and plastic in critical applications due to fiber-based materials having a better balance between their strength and weight. Similarly, graphene has the potential to improve fiber composites in a variety of ways.
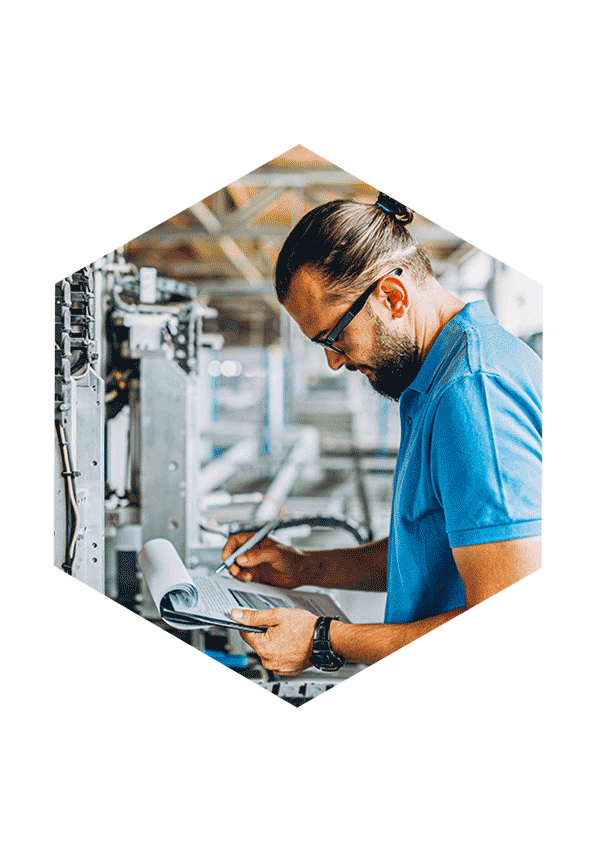
Developing Enhanced Composite Formulations with Graphene
Although fibers carry most of the load in composite materials, their matrix is also essential in keeping fibers together and transferring the load. By enhancing the matrix, graphene offers the potential to improve resins used in composite material manufacturing. For example, graphene nanoplatelets in the matrix inhibit crack formation and propagation due to shock or catastrophic load. Graphene-enhanced composites also exhibit higher fatigue resistance and impact resistance compared to conventional alternatives. G6 is working to develop enhanced composite formulations to make graphene’s benefits available to customers via easy-to-implement solutions.
Our Solutions
Contact G6 for General Inquiry
Contact our business team, request details on products, or ask a technical question.
Call to Inquire | 516-382-8649 760 Koehler Ave. Unit 2 |
Ronkonkoma, NY, 11779 | USA Copyright © 2022 G6 Materials Corp, All Rights Reserved Disclaimer & Terms of Use